
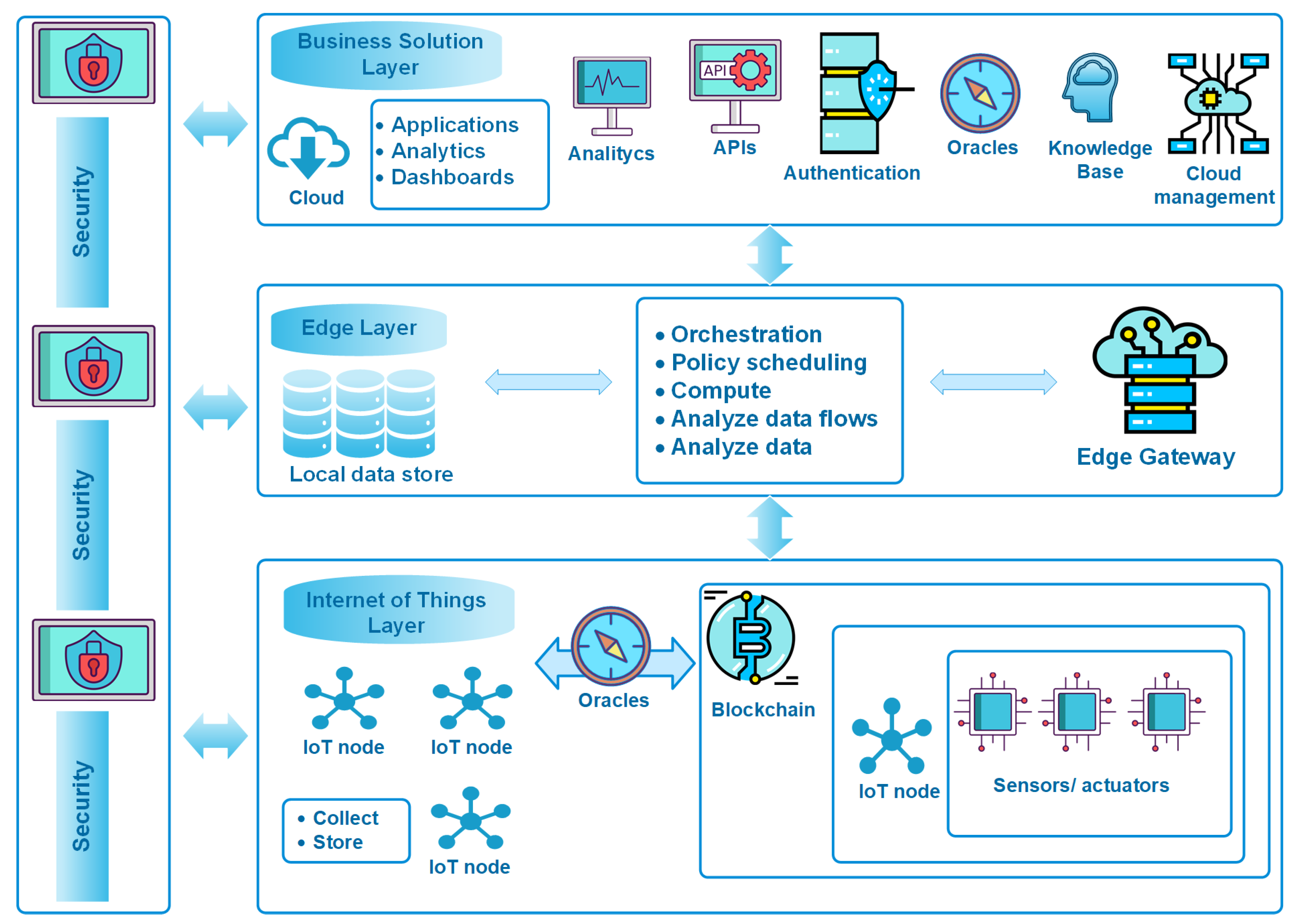
Here are the main reasons why a walk around program does not constitute a truly predictive maintenance solution. However, this traditional approach of once a month data collection is not truly predictive as it comes with several limitations. A technician goes around the plant periodically and collects sensor data using a data collector. However, this is a very expensive solution and is often reserved for the small percentage of the most critical machines.įor the balance of plant equipment, predictive maintenance has typically been conducted using a walk around program. In continuous monitoring, wired sensors are installed on the machines are connected back to the asset management software. To determine the health of the machines, sensors are used to measure various machine parameters such as vibration, temperature and ultrasound. Predictive Maintenance is referred to the maintenance approach of understanding the underlying “health” of a machine to determine if a corrective action is required. In either of these approaches, the focus is not on assessing and predicting machine condition. Also, improper PM can lead to unintended malfunction. These schedules can be unreliable because the actual operating condition of the machine may be different from the recommended operating condition. Work order schedules are often based on manufacturer’s recommendations.
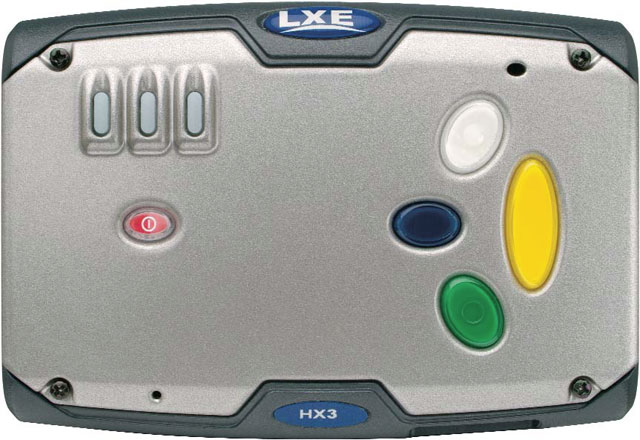
Under a preventive maintenance approach, maintenance teams create predefined repair schedules without considering the actual condition of the machine. Ideally run-to-failure is recommended for the least critical assets which have very little impact on operations. This leads to unplanned downtime and significant repair costs. In a reactive model, a machine is repaired or replaced only in the event of a failure. Traditionally, most factories have adopted either a reactive (run-to-failure) or a preventive maintenance (PM) model because of the high costs of predictive maintenance. Run-to-Failure and Preventive Maintenance This article compares and contrasts the traditional models with the modern IoT-based PdM approach. According to ARC and others, predictive maintenance is currently the biggest use case for IoT across all sectors.

This trend is called the Industrial Internet of Things (IIoT). Companies are making use of these technologies to offer an end-to-end, easy-to-deploy PdM solution at extremely affordable price points. However advancements in wireless, cloud and AI technology are disrupting the way PdM has been done in recent decades. Traditional PdM methods have several limitations. In today’s competitive industrial world, predictive maintenance (PdM) is no longer a nice-to-have it has become a necessity.
